
Yates Hoistroom
Anyone who has driven through Lead, South Dakota has seen the iconic Yates Headframe standing high atop a mountain. The headframe stands over a mile-deep shaft and houses the pulley system for the cages. The Yates cage easily makes up to twenty trips up and down the shaft daily, delivering people and supplies to different levels of the facility. The real power, however, rests in the Yates Hoistroom, an unassuming brick building sitting just a few hundred feet from the base of the towering headframe.
“It’s a feat of engineering, to be sure,” said Martin Brosnahan, who maintains facility infrastructure at Sanford Lab. “It’s astounding how Homestake engineers in the 1930s were able to create such a reliable, durable system that we still operate today.”
Built in the 1930s, four of the original seven Nordberg hoists are still in use today by Sanford Lab, and two of those are in the Yates Hoistroom. Sanford Lab is the only facility in the world operating hoists with this specific design, which was patented by a former Homestake employee. But how does it work?
Round and round
The Yates Shaft is 5,000 feet (1,524 meters) deep. Inside the shaft, the cage hauls people and supplies from the surface to the 4850 Level and back. The cage is connected by a bonnet to a 6,000-foot (1,829 meter) hemp and steel rope. These ropes, nearly two inches thick, feed through a pulley system at the top of the Yates Headframe, then run directly to the drums in the Yates Hoistroom. The ropes wrap around the drums in just one layer, decreasing friction and wear, and extending the life of the rope.
The drums, shaped something like massive spools of thread, have a unique design. One end of the drum has a diameter of 25 feet, but the design tapers, narrowing to a diameter of 12 feet.
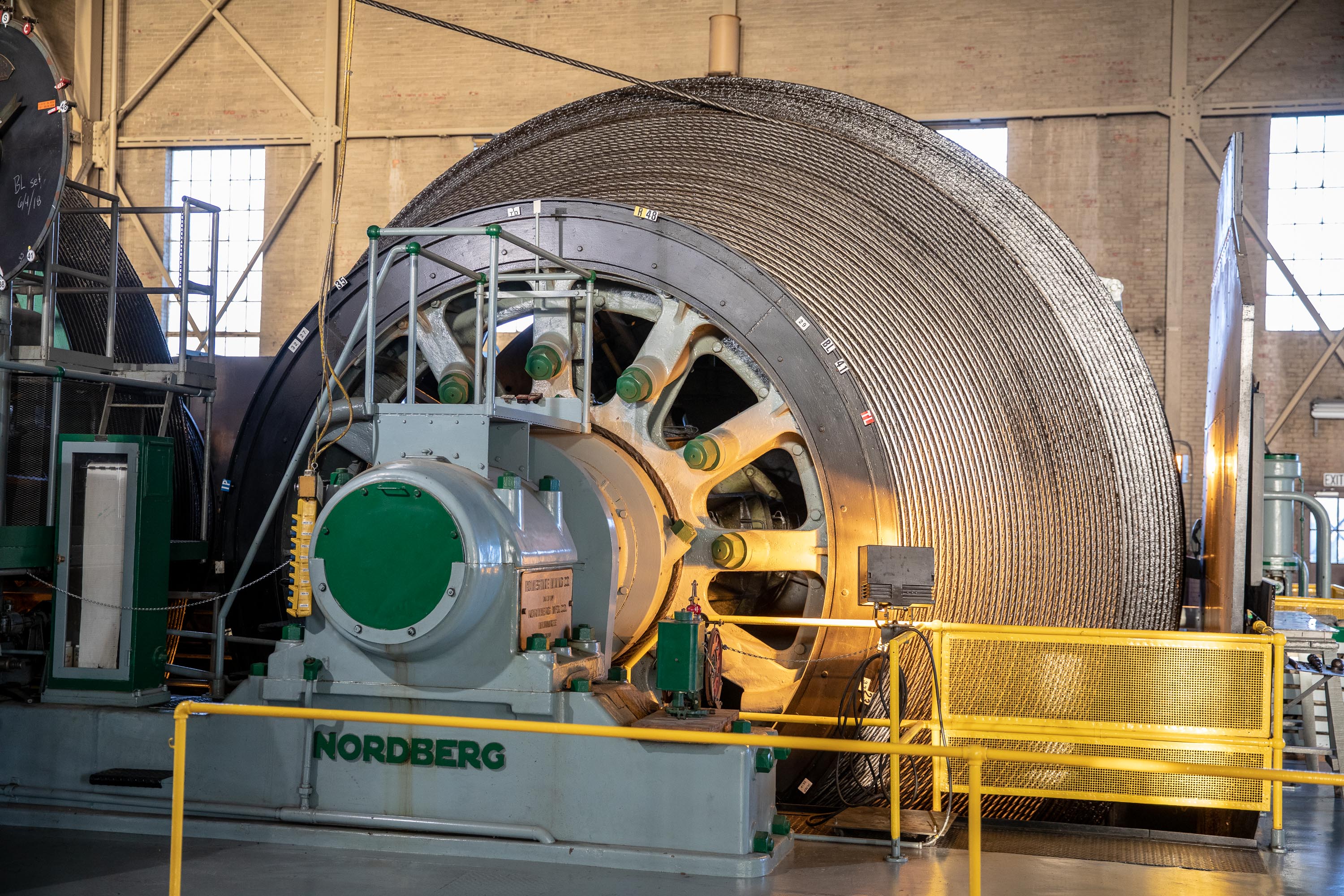
“As the diameter of the drum changes, it has a similar effect to changing a gear ratio on a mountain bike,” explained Greg Crotty, a Yates Hoist operator who has been operating this system since 1986. “The small diameter on one end gives you more power as you’re pulling a load out of the bottom of the shaft, and then less power at the top when the diameter is wider.”
At each hoist, two drums sit side-by-side and run in tandem. Together, they create a counterbalancing system. As the operators lower one cage, the weight of it lifts the other. While the drums can be run separately, running them together greatly reduces the energy needed to power the hoists.
So what makes these drums turn?
A steel shaft weighing nearly 30 tons runs through the center of each drum, supporting the drums, the rope and the load on the cage. The shaft fits snugly into bearings, where it is doused continuously with circulating oil to keep everything spinning smoothly.
The spin of this shaft is driven by the main drum shaft gear. This large gear, boasting 214 pinion teeth, is clamped around the shaft. A gear-reduction system propels the main drum shaft. An important piece of this system is the large idler gear. This gear connects the gear systems of the two drums running in tandem, ensuring each system is spinning at the same speed.
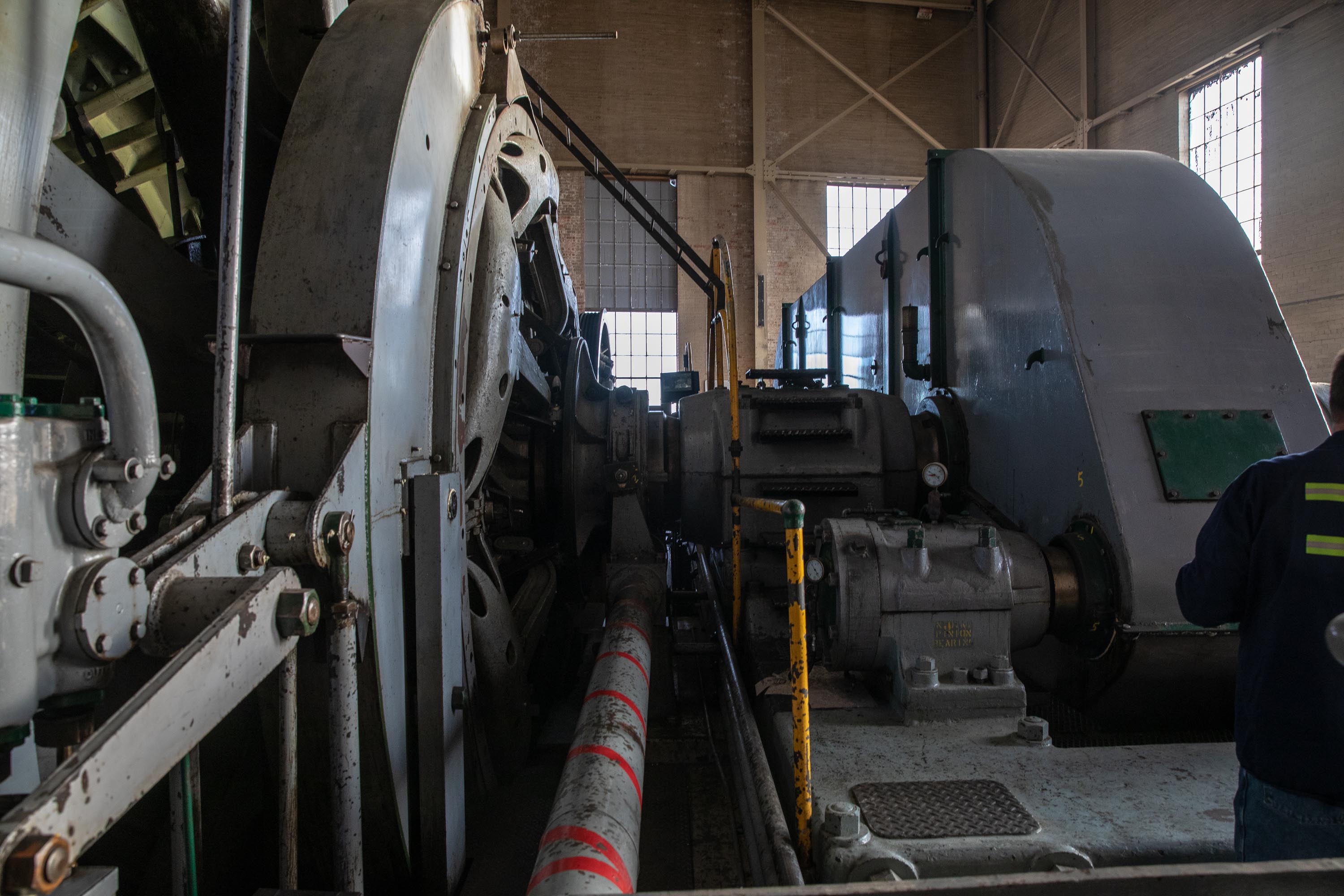
So, gears turn gears, which spin the shafts, which rotate the drums, which lower and raise the cage. Brilliant. But what sets the system in motion? Energy. And lots of it.
Powering the system
Energy is delivered to the Yates Hoistroom as alternating current (AC), but direct current (DC) is needed to power this massive machinery.
“When a cage is resting a mile deep in the shaft, it takes an immense amount of energy to begin lifting it up,” said Paul Bauer, electrical project engineer at Sanford Lab. “The power-torque characteristics of a DC motor are better suited for this job. The motor can begin slowly turning from a dead stop, while still providing sufficient torque.”
An entire room in the Yates Hoistroom is dedicated to converting AC power to DC power. Two motor-generator sets, one for each of the hoists in the Yates Hoistroom, run constantly. Each AC motor receives 2,300 volts of energy from the substation. That motor couples to a DC generator, which creates anywhere from 0-600 volts of DC energy at a time. This DC generator feeds into both the hoist motors and a 50-ton flywheel.
“The flywheel is incredibly important, because it stores excess energy created by the DC generator. When you start moving the hoist from a complete stop, you need a whole bunch of power in a short amount of time to get it moving,” Bauer said. “That initial burst of energy might use 3,000 horsepower over a very short time. The flywheel supplies that excess energy.”
The DC motor also feeds into two hoist motors, each 1250 horsepower. These motors make the gears on the drums go around.
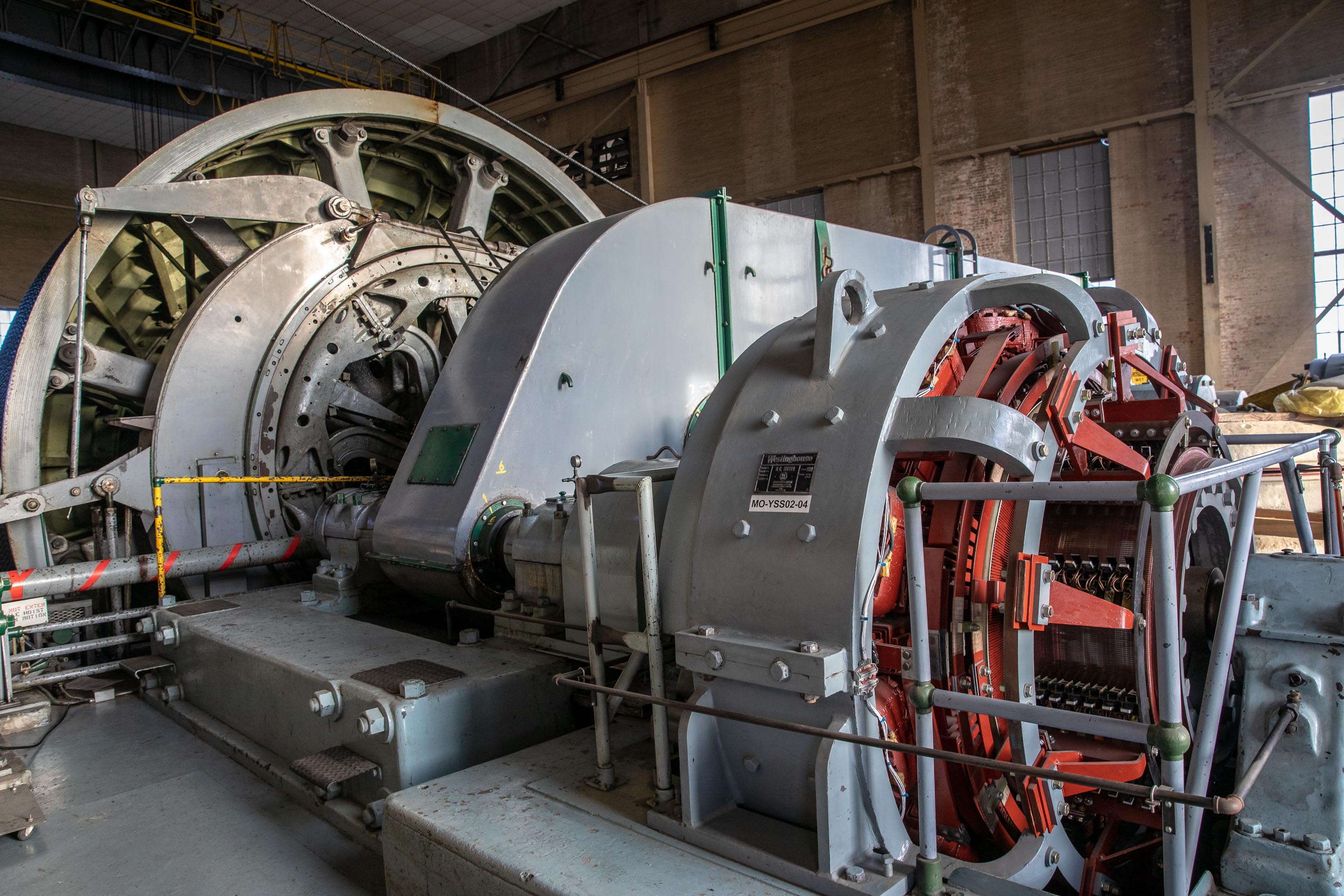
Slowing it down
With this combination of energy and torque, how do you slow things down? With large break shoes fixed around a rotating disc called a break drum.
The brake shoes are composed of two half circles of bass wood with a diameter of 14 feet. When the operator applies the break, a large arm, aided by gravity, presses the two shoes against the break drum, pinching, slowing and stopping the motion of the drum.
In an emergency, multiple safety measures can stop the cage in the shaft. A mechanically driven automation control, fittingly named a “slowdown,” will slow and stop the hoist automatically if the cage nears the top or bottom of the shaft. Additionally, a mechanically driven Model C Lily controller monitors the emergency braking deceleration rate. Should the cage descend too quickly, the Lily controllers will automatically slow and stop the cage.
Both the slowdowns and the Lily are separately driven from a single gear mounted on the main hoist drum shaft. Although they are driven from the same gear, their drivetrains are separated, allowing them to monitor the movement of the drums independently.
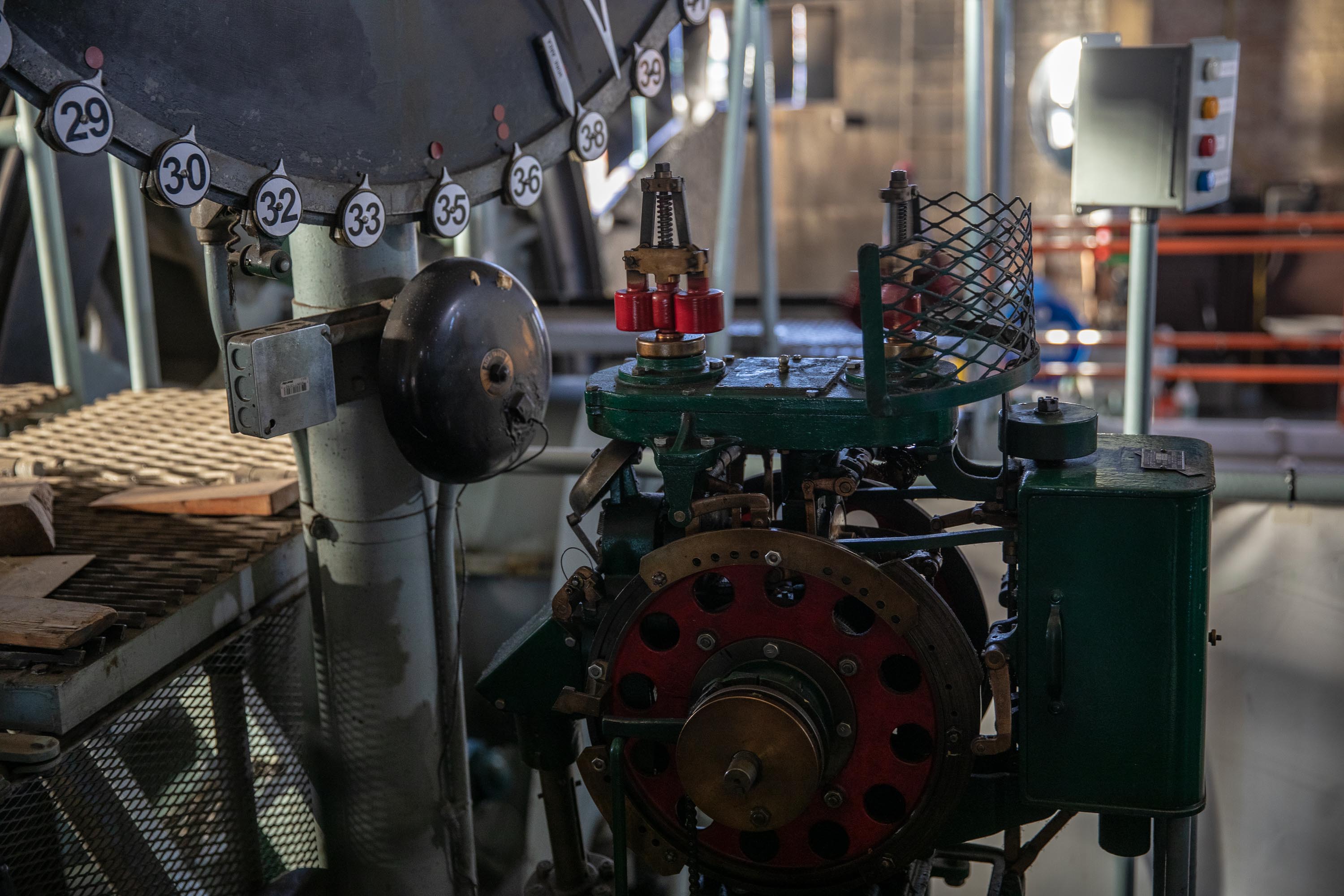
The control room
Operating the only Nordberg drums of their kind in the world requires specialized skills. Because the system is controlled manually, hoist operators are essential to operations at Sanford Lab.
The hoist operator sits on a raised platform, in full control of a hoist system. Before him are the break controls, clutches and throttle. Small dials indicate oil pressure and power levels. Beyond the platform, large dials indicate the location of the cages in the shafts.
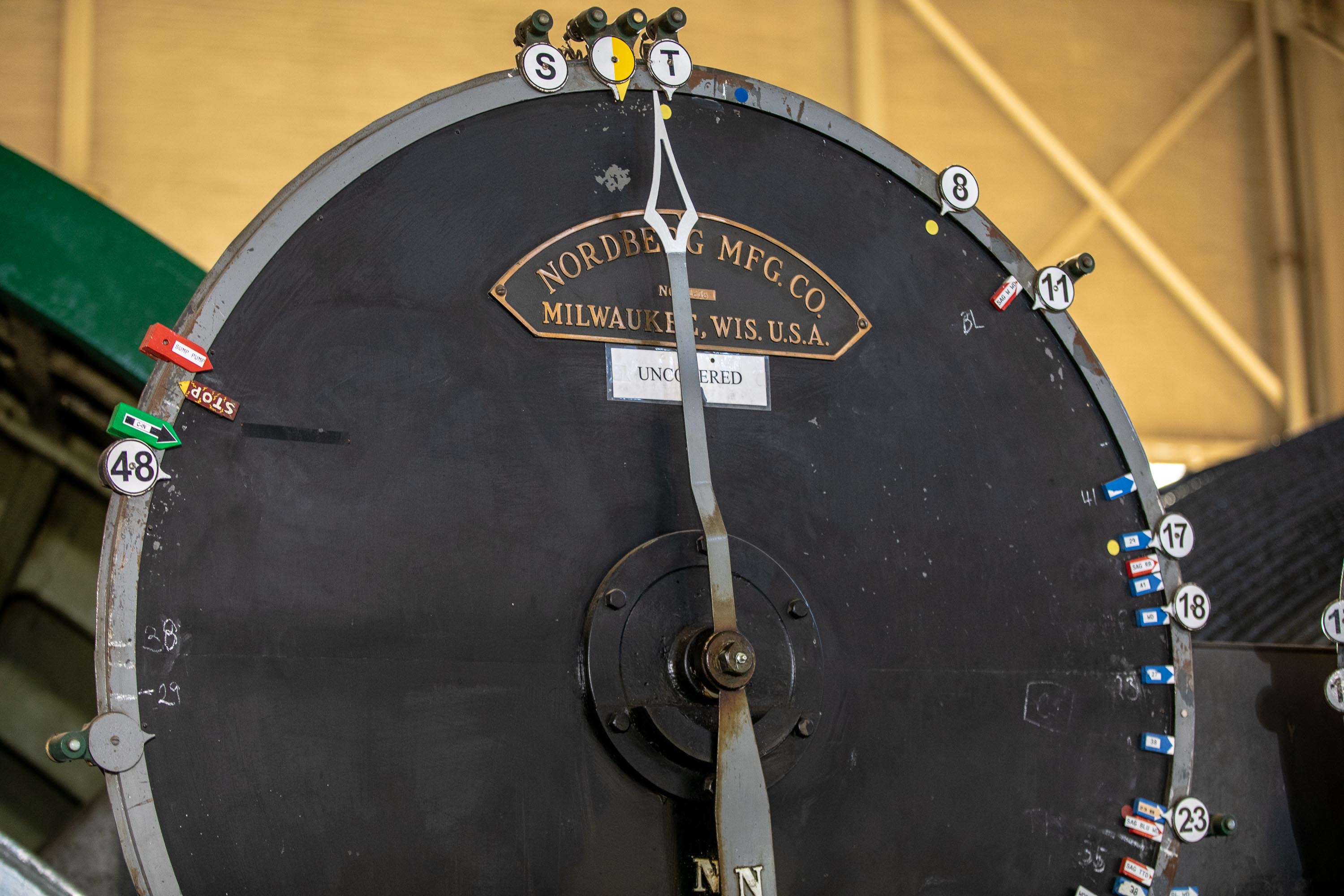
The hoist operator is in constant communication with the cage operator, who gives the order to start and stop the conveyance and provides instructions to rest the cage on chairs if necessary.
“Communication is very important,” said Crotty from his seat on the operator’s platform. “I’m in control of everything they are doing. We need to communicate together so we’re on the same page, so I'm doing the right thing.”
Putting it all together
From the powerful generators converting energy to the uniquely designed drums, the Yates Hoistroom is a powerful picture of the hoisting power required to keep science running. The longevity of the hoists is a testament not only to the care given through regular maintenance, but to a time when things were just made well, Crotty said.
“This system was put in in 1939, and it still works well,” said Crotty. “The American ingenuity in those days was amazing, and they built sturdy stuff. This hoist system is a testament to this.”