Milestone reached in Yates Shaft top-down maintenance
Infrastructure crews reach 4850 Level in the skip compartments of the Yates Shaft
Infrastructure crews at Sanford Underground Research Facility (Sanford Lab) reached a major milestone in their effort to enhance the infrastructure of the Yates Shaft. This March, crews completed top-down maintenance from the surface to the 4850 Level in the skip compartment of the Yates Shaft.
“This project has been in the works for a long time, and we are thrilled to see these milestones bringing us closer to completion of the overall project,” said Mike Headley, executive director of Sanford Lab.
As the main conduit for transporting people and supplies underground, the Yates Shaft is often considered the facility’s “interstate to the underground.” Since 2012, infrastructure technicians have worked to provide consistent access to various levels, while working to reinforce the integrity of the structure.
“The Yates Shaft crews are experts at methodically executing the top-down maintenance program, and it is a big accomplishment to complete the skip compartments to the 4850 Level,” said Bryce Pietzyk, underground access coordinator. “I also want to recognize all the work it takes from other departments to keep the program moving, including finance, accounting, purchasing and safety.”
An eight-year effort
Construction on the Yates Shaft began in 1939. Because the nation’s steel supply was dedicated to the early war effort, Homestake Mining Company constructed the Yates Shaft out of timber, unlike the Ross Shaft, which had been built with steel five years prior.
A feat of engineering, the 5,000-foot structure is comprised of 799 stacked support sets that divide the shaft into three main compartments: the North and South cages, which transport people and supplies between levels; the North and South skips, which hauled ore from underground; and the utility compartment, which houses piping and electricity lines.
When Sanford Lab reopened the Yates Shaft, work began to ensure the longevity of the shaft. In 2013, leadership developed a methodical construction approach called “top-down maintenance.”
Top-down maintenance involves inspecting every component of every set, giving each a “grade,” said William McElroy, executive operations program manager. McElroy, who was the underground access director at the time, helped develop the maintenance project. Timbers, posts, guides, bolting, lacing and turnbuckles are all examined and graded. This information is compiled into a database that details the health of each of the 799 sets in the Yates Shaft.
“Data tells a story,” McElroy said. “When you have nearly 800 sets with so many individual components, you need data to inform your decisions.” The data guides infrastructure crews as they move from the surface and work their way down the shaft, set by set.
But top-down maintenance involves more than rating and making needed repairs. As the crews move down the shaft, they also remove the old wooden lacing and 75 years of muck (rock, timber and gravel) that has built up behind it.
“Regular rock removal equipment doesn’t fit in the cage compartments, so removing rock is done by hand, using a flat shovel and five-gallon pails,” said Casey Schaff, Yates Shaft foreman. “Those pails are dumped into the skip, which can hold 11 tons of material, and hauled to the surface at the end of the shift.”
On average, crews remove more than 27 tons of muck every month. As the muck is removed, crews put in new ground support, repair timber pieces and install new lacing where needed.
Achieving the milestone
In 2019, infrastructure crews completed maintenance on 677 sets in both the cage and the skip compartments of the Yates Shaft. This brought their progress to just below the 4100 Level. They then focused their efforts on the skip compartment, in anticipation of an upgrade to the skip hoist motors that would temporarily pause maintenance in the skip compartment. This March, the crew reached Set 767 at the 4850 Level in the skip compartment.
Including post work, guide work, bolting, lacing and blocking, there have been 28,696 corrections made in the Yates Shaft to date. While performing all of this work, the Yates Shaft crews have also moved 4,800 loads since January 2018.
“During this project, we’ve had no lost time or injuries. I attribute that to the diligence of the crews working in the shaft,” said Patrick Urbaniak, Yates Shaft superintendent. “They do a good job of looking after each other and looking after other crews, too.”
“Top-down maintenance will now continue in the cage compartments just below the 4100 Level and eventually continue in the utility compartments,” Pietzyk said.
The overarching vision
On the other side of the facility, the Ross Rehabilitation project, a complete rebuild of the shaft’s steel infrastructure, is in the final stages. In terms of facility progress, McElroy says the Ross and Yates Shafts must be considered as a pair, rather than separate systems.
“These two shafts are the access points that make every other part of our work possible,” McElroy said. “Whatever you do with one will impact the other. This has to be the vision for the future of what we are doing here.”
As Sanford Lab leadership considers future plans for the Yates, including an imminent rebuild of the shaft with steel infrastructure, McElroy said the top-down maintenance project will help with that work.
“The lion's share of rock bolting in the shaft will be completed during top-down maintenance, which is a massive, massive advantage to future work in the shaft,” McElroy said.
Keeping maintenance at the forefront
Most everyone who travels down the Yates Shaft has passed a yellow railcar outside the Education and Outreach building on their way to the ramp. The railcar is filled with rock from the Yates Shaft. McElroy was a proponent of placing the railcar in this central location, as a tribute to the vital maintenance processes at Sanford Lab.
“I wanted it to be a constant reminder of how important ongoing maintenance is in the Yates Shaft,” McElroy said. “The time that is dedicated to maintenance is so important to the future and longevity of our entire facility—and to the safety of our team.”
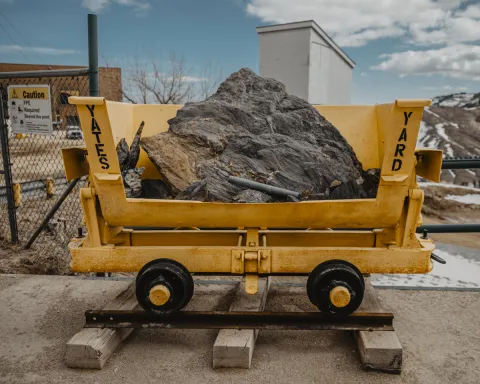